In March, 2024, I flew to California to help an elderly cousin. While cleaning the garage, I stumbled upon an old Unimat lathe in a wooden box. I had no time to inspect it further, so I took a few pictures and set it aside for another time.
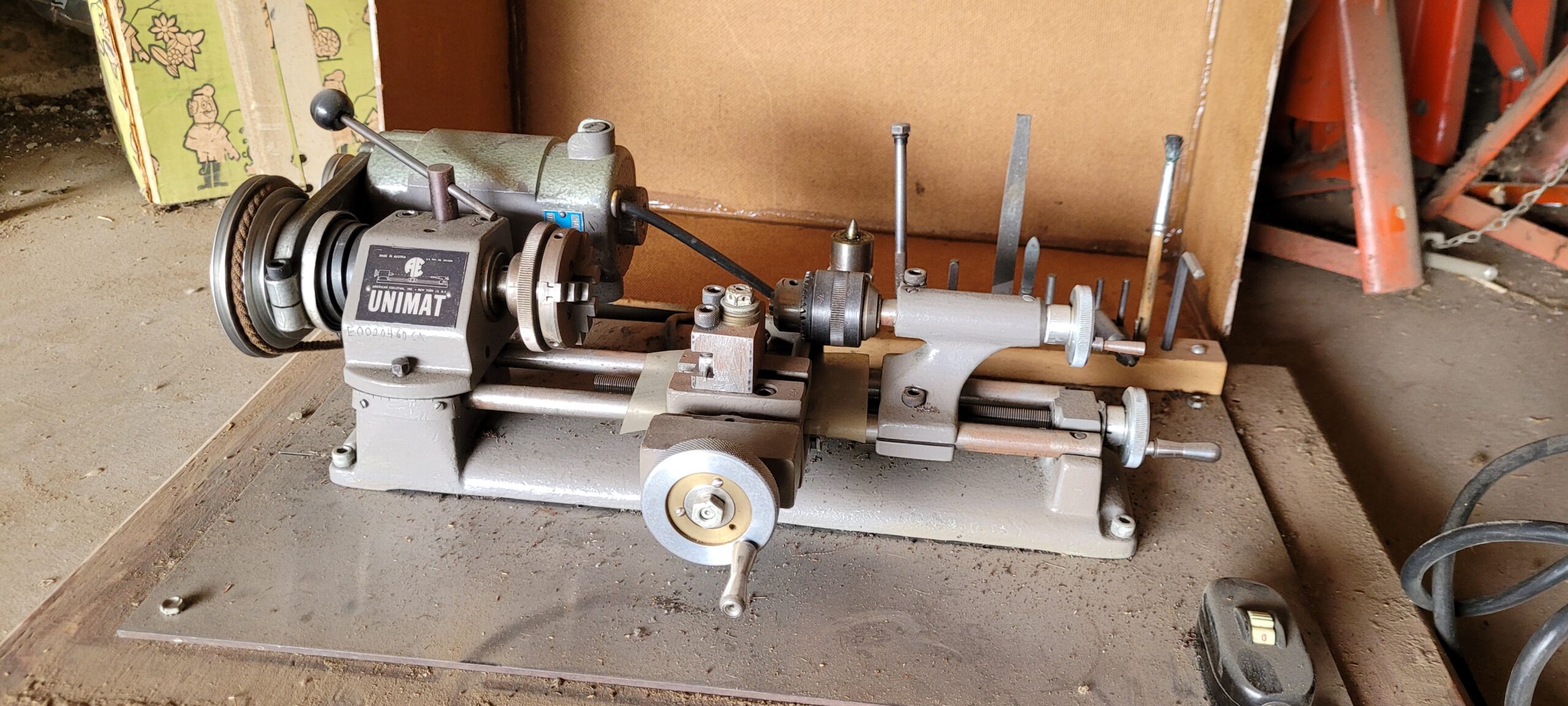
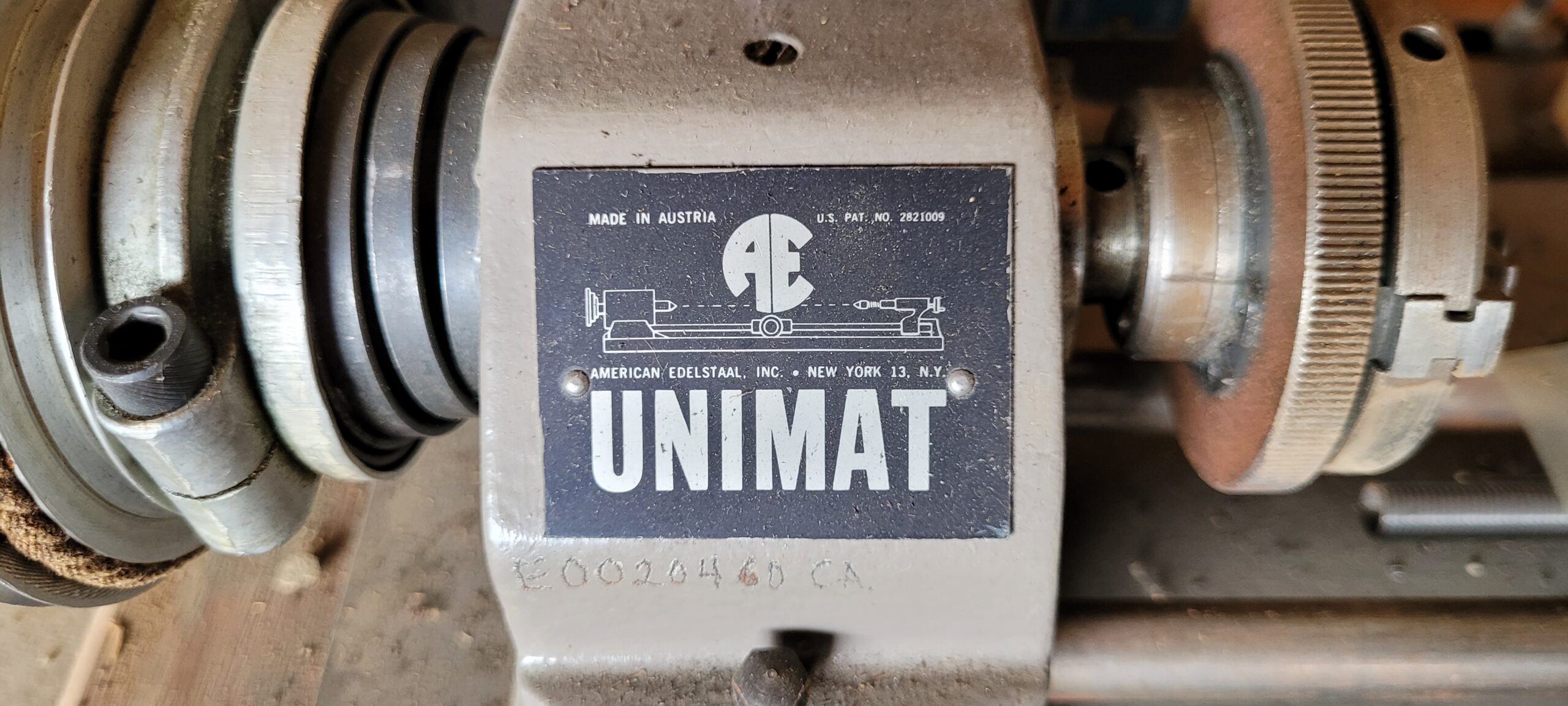
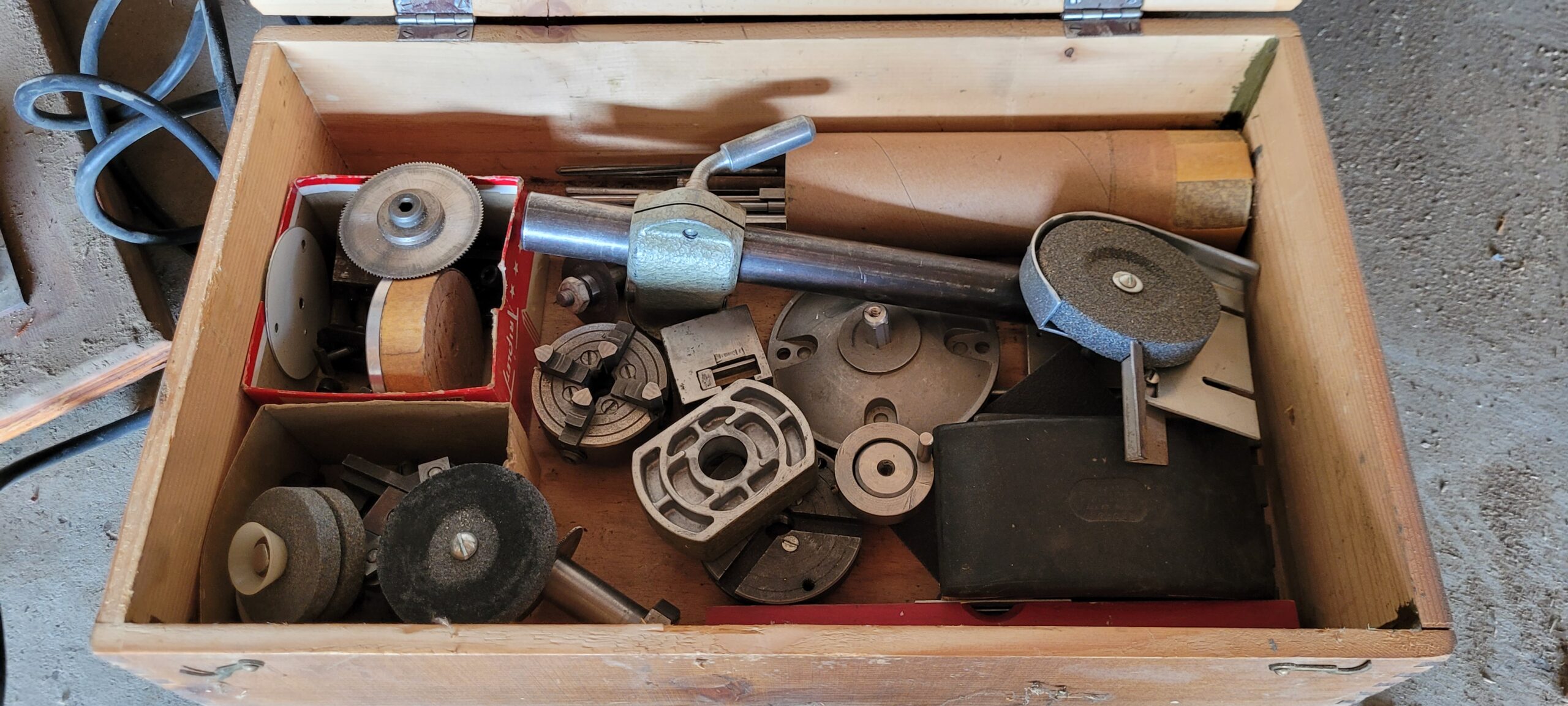
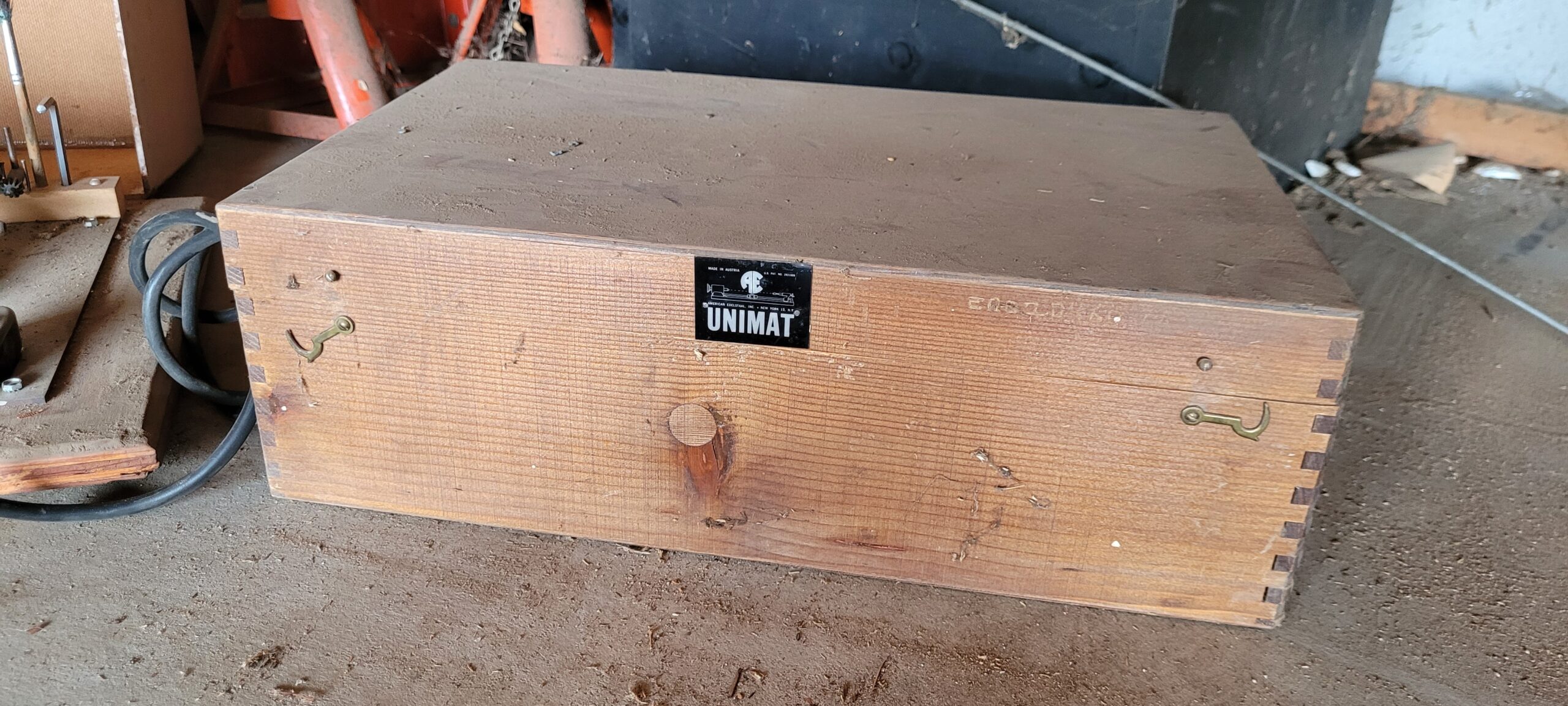
When I returned home I did some research on the little machine. It was a Unimat DB200. Unimat stands for “UNIversal MAchine Tool”, as it can be configured as a lathe, a milling machine, a drill press, and many other tiny power tools. This one had a heavy base of cast iron, which makes this an earlier model. I already had a much larger Grizzly lathe, but I thought that this little Unimat could be useful for tiny work. I thought it would make for a fun restoration project, too. I watched countless videos about the Unimat to become more familiar with its operation and capabilities.
When I returned to California 6 months later, I asked about the lathe’s history, but my cousin had no recollection of it and told me to take it. I shipped the Unimat back to Michigan on September 12, and it arrived September 18. It had both a 3-jaw scroll chuck and a 4-jaw independent chuck, in addition to a face plate and clamps to hold irregular objects. It had a Jacobs chuck and a live center for the tail stock. The original tool holder still had a high-speed steel cutting tool in it. My goal for the project was to return it to as close to original condition as I could. Many hobbyists seem to replace the original motors with larger, more powerful units, but I wanted to retain the original compact size and appearance. The little 90 watt motor would suffice.
On October 10, I completely disassembled the lathe to assess what I had. There were some damaged and worn pieces, which I found replacements for on eBay. I also made a few replacement pieces on my larger lathe. At some point in this tool’s long history, somebody repainted it in a dull tan-gray primer. The cross-slide was previously molested by a drill, and an ugly block of metal was added to it for reasons unknown. The main spindle bearings and races were in surprisingly great condition, but the pair of small ball bearings for the idler pulley were frozen solid, so replacements were ordered. I don’t plan on doing much, if any, milling with this tiny tool, but I ordered a replacement milling table to replace the original that had a chipped corner. The original belt made from braided rope would certainly be replaced. Both the main and cross slide lead screws were slightly bent, so I ordered replacements for each. Every part was ultrasonically cleaned.
I wanted to repaint it using a hammered green paint that was similar to the original finish, but this color was available only in a brush-on paint. I opted for a hammered copper color spray paint instead. The layers of paint were chemically stripped away, then all painted pieces were masked and primed before the hammered copper paint was applied. I made new aluminum rivets for the faceplate.
Reassembly began on October 26 and finished the following day. The Unimat ran again for the first time in decades. I still need to use my dial indicator to ensure that the cross slide tracks true and that the head stock has minimal run-out, but otherwise, the lathe is back together. The wooden box still needs reconditioning, but that will be a project for another time.
I’m quite happy with the results of this project. For fun, I set the tiny Unimat on my Grizzly lathe for a quick picture to compare the size difference. While the Grizzly will get most of the lathe work, the Unimat will be ready for any future micro-machining needs.
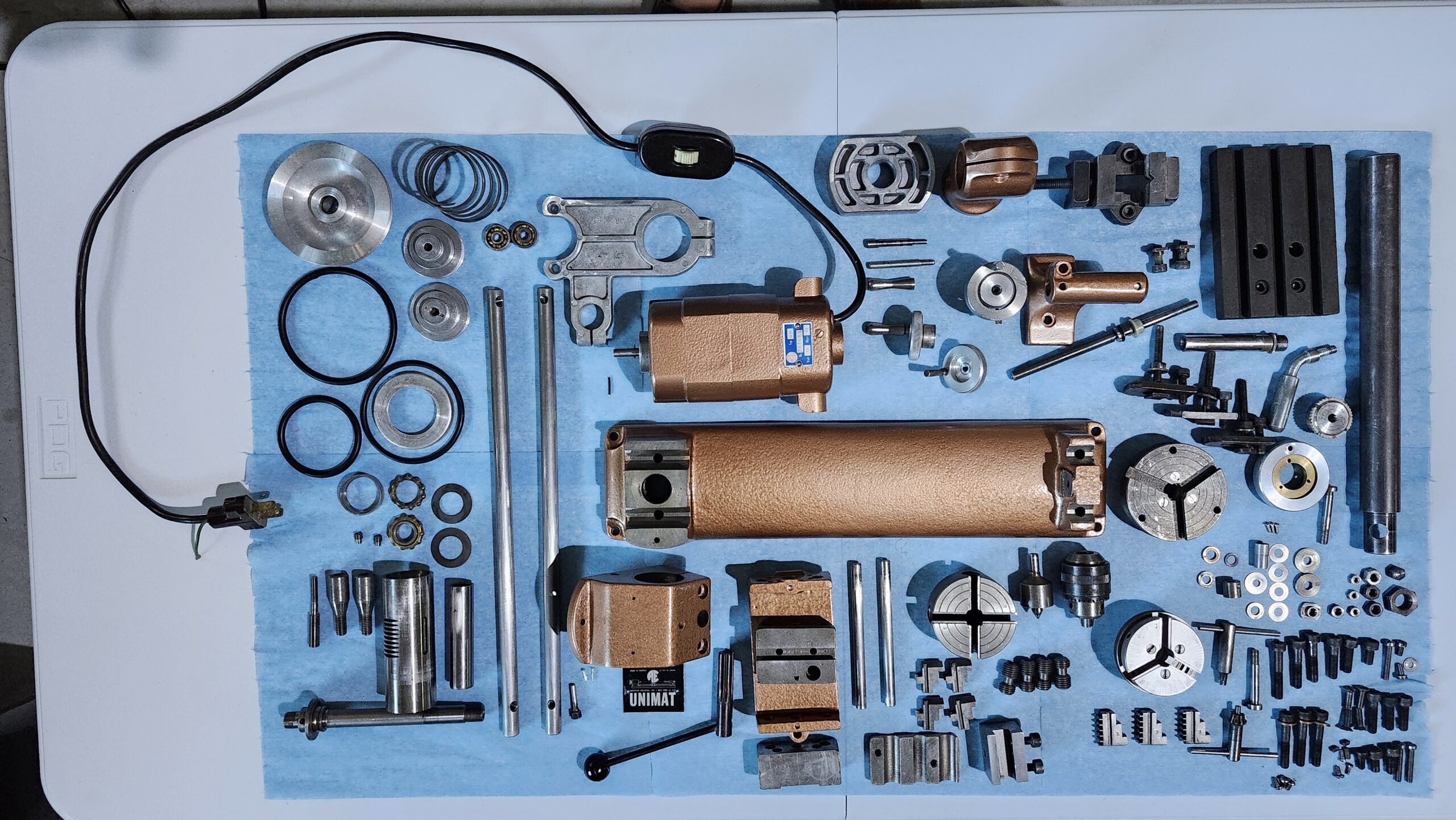

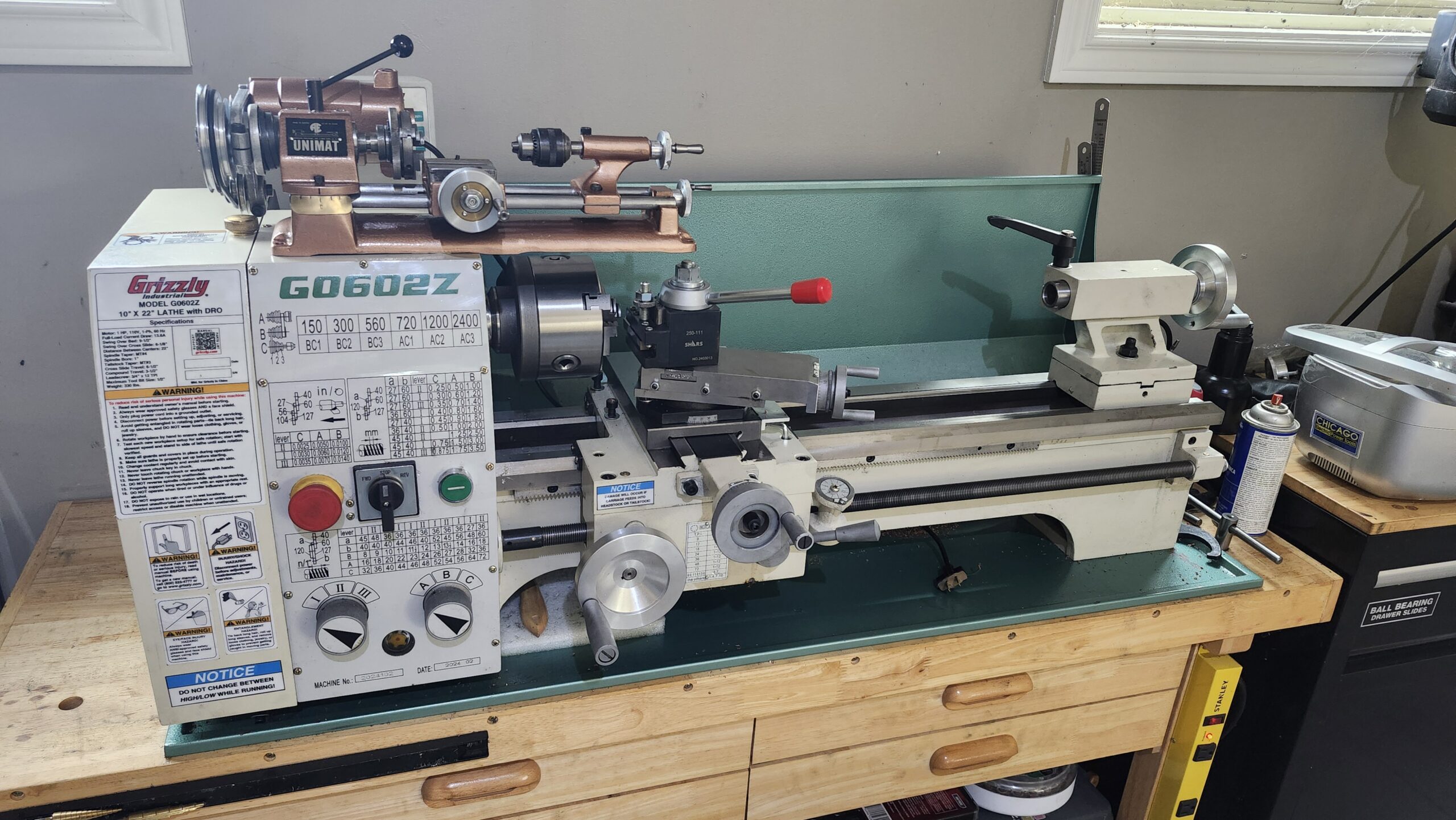
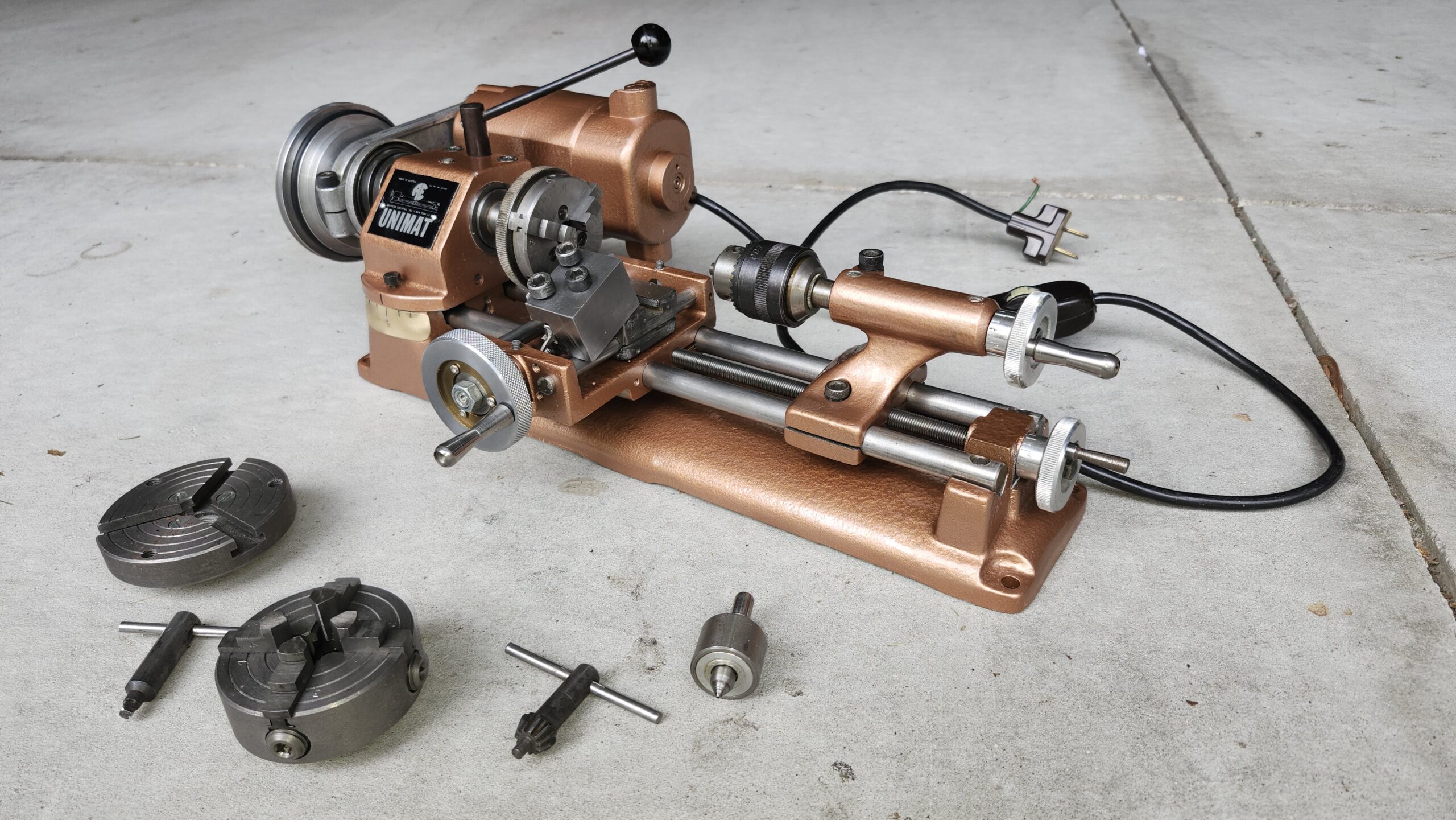
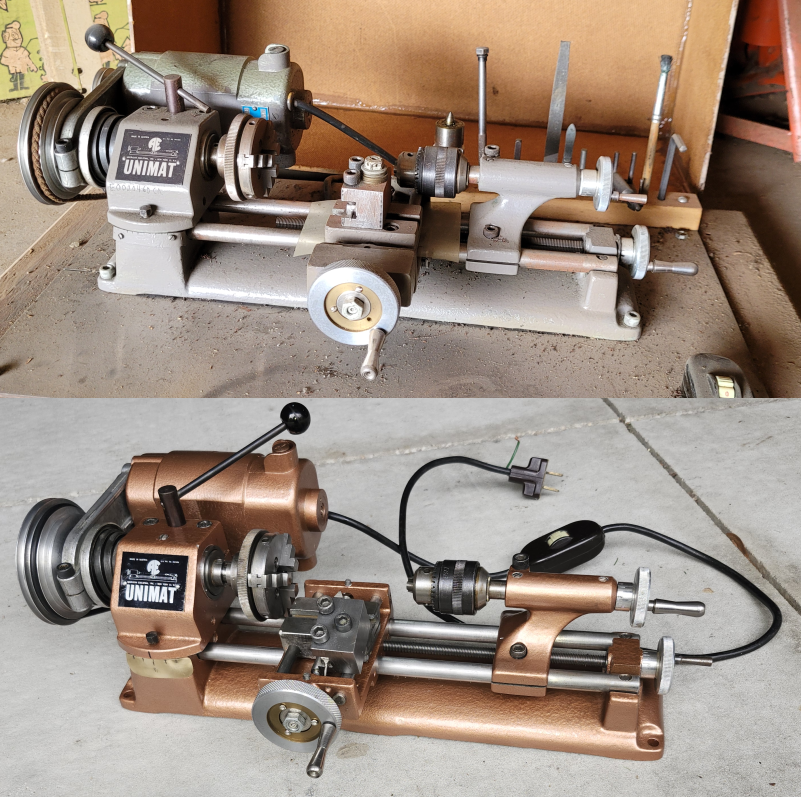